10 - Maintenance Operations
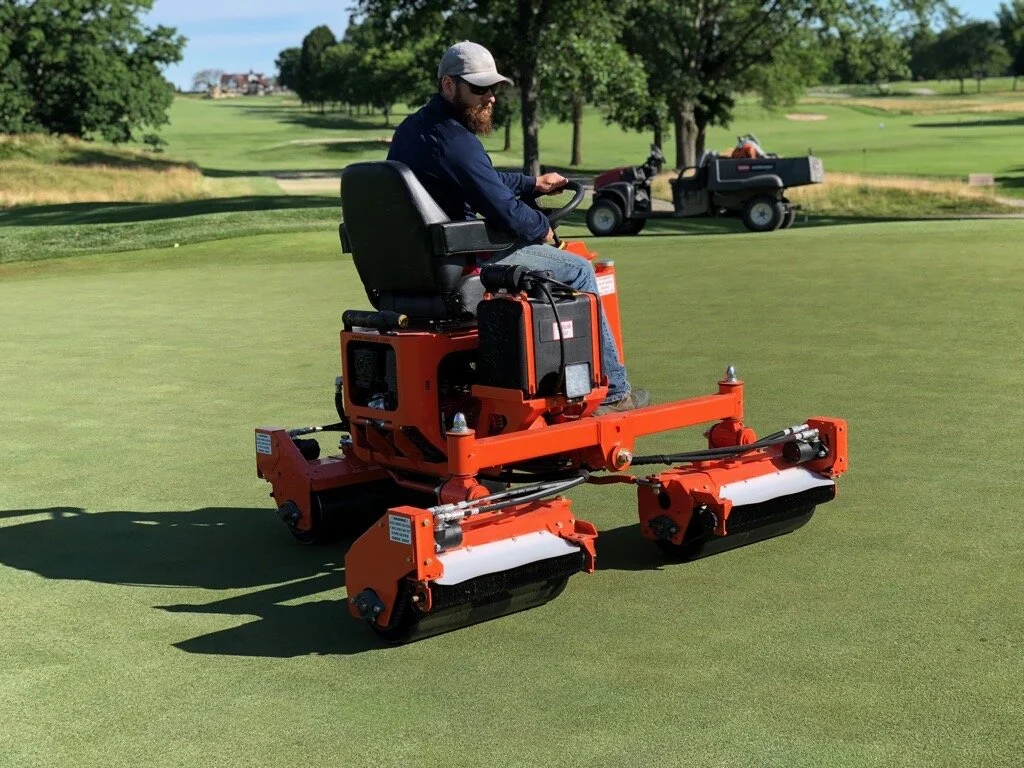
Maintenance operations and facilities should support employee wellness, safety, productivity, and performance. Facilities should include areas for employee training, equipment maintenance, and storage of chemicals, fertilizers, fuel, plus other maintenance items.
Regulatory Considerations
Early engagement amongst developers, designers, community groups, and permitting agencies is essential to constructing a golf maintenance and storage facility. Local and regional regulations may be in place by municipality or county. Consult the proper regulatory officials to determine requirements.
It is important to ensure proper handling and storage of pesticides and petroleum-based products to reduce human, environmental, and economic risks including the potential for serious injury to operators or bystanders, environmental contamination, fines, and cleanup costs. Resources for state regulations are noted in each subsection.
Wisconsin’s statewide recycling program is governed by Wisconsin Statutes, Chapter 287 and related administrative rules found in Wisconsin Administrative Code (Chapters NR 542 to 549). For an overview of the state program reference: https://dnr.wisconsin.gov/topic/Recycling/law.html
Maintenance Operations protocols should be in place to minimize environmental impact and promote the health and safety of individuals.
Maintenance Facility
Maintenance facilities should accommodate dining and break areas for staff, storage for equipment and supplies, and the mechanic’s areas. All areas should be properly ventilated and well-lit. Numerous activities should be considered to support water, energy, and cost reductions:
Restrict water flow to the maximum necessary for adequate use
Use automatic shutoffs on faucets
Install 1.5-gallon tanks on toilets
Use motion detectors to turn on lights when staff is present
Employee Break Room and Training Area
Maintenance facilities should include an employee lunch/break room, which often serves as a professional training area for technical education. The area should be clean, organized, and provide a relaxed atmosphere. The size of the golf course operation and number of maintenance crew employees will determine the appropriate size of the lunchroom. There should also be adequate space for administrative and managerial offices as well. Important items to include:
Adequate tables/chairs for dining and training
Microwave oven (reduces time for meal preparation)
One adequate-sized (energy saver) refrigerator
Drinking water with dispenser, coffeemaker, refreshment vending machine
Kitchen area with sink, water, sufficient cabinet area
Adequate space including light, easy-to-clean colors/walls
Organized food and utensil storage with labeled containers and easy-to-access shelves
Erasable or electronic communication board
Air conditioned and insulated, with overhead fans for air flow
Mechanics Workshop and Office
Equipment is serviced and repaired in the mechanics workshop – it must be designed with adequate space for oil changes, reel grinding, and other jobs. An assortment of lifts (portable, flush floor mounted and beam supported) should be utilized, when available, to assist with moving equipment and minimizing risk of injury. If practicable, an overhead lube center (grease/oil dispensers supported by compressed air and connected to bulk drums) reduces the need for floor space and stores drums out of the work area. Empty gas cans, towels and miscellaneous supplies can be stored in cabinets throughout the shop. A sink and hand dryer should be available in the shop. Ensure combustible products are stored in fire resistant cabinets.
Large work benches provide ease for working at waist level and can decrease risk of back injury. An air-conditioned office with desk, computer, files, phone, and storage should be adjoining.
Storage Areas
Chemical Storage
An IPM Control Center is a lockable concrete or metal building designed for storage of pesticides. It should be located away from other buildings, especially fertilizer storage facilities.
The fertilizer storage structure should be large enough to facilitate logistics, allowing a small forklift to deliver fertilizer by pallet. If the building is constructed of metal, then the metal should be protected from degradation by fertilizer (such as adding painted plywood around the walls). When maintaining the building, employing a dehumidifier can help protect fertilizer from water absorption.
Best Management Practices
Place appropriate warning signs within and outside of storage buildings
Store PPE away from pesticide storage in an easily accessible area
Follow all PPE statements on pesticide labels
Develop an emergency response plan and educate personnel regarding emergency procedures on a regular basis
Individuals conducting emergency chemical cleanups should be properly trained under requirements of the Occupational Safety and Health Administration (OSHA)
Detailed records of current pesticide inventory should be maintained in the storage facility
SDS for chemicals stored onsite should be readily accessible and stored separately from the storage room
Follow a “first in, first out” principle to rotate products into use and ensure products do not expire. Do not store large quantities of pesticides or chemicals for long periods
Store chemicals in original containers; never store in containers that might be mistaken as packaging for food or drink
Arrange containers so labels are clearly visible
Securely fasten loose labels to ensure containers and associated labels are kept together; damaged labels should be replaced immediately
Store flammable pesticides separate from nonflammable
Store liquid materials below dry materials to prevent leaks from contaminating dry products
Incorporate impervious floors sealed with chemical-resistant paint within chemical storage buildings
Floors of chemical storage buildings should have a continuous sill to contain spills and should not have a drain; a sump is acceptable
Shelving should be fabricated from plastic or reinforced metal (painted to avoid corrosion); at least six feet off the floor; wood shelving should never be used.
Automatic exhaust fans and an emergency wash area should be provided
Explosion-proof fan and lighting may be required
Ventilation design must be integrated; locate fan and light switches outside the building entrance to facilitate ventilation before staff enters the building
Ensure oil containers and small fuel containers (service containers) are properly labeled and stored within the facility
For information about constructing chemical mixing facilities, reference the Midwest Plan Service book, Designing Facilities for Pesticide and Fertilizer Containment (revised 1995); the Tennessee Valley Authority (TVA) publication, Coating Concrete Secondary Containment Structures Exposed to Agrichemicals (Broder and Nguyen, 1995); and USDA–NRCS Code 703
Reference Responsible Pesticide Management for additional pesticide storage BMPs.
Soil Storage
The soil storage area should be covered with a roof to prevent rain or moisture from reaching the soil and wind from dispersing weed seeds into topdressing. The area could be located in proximity to the fertilizer storage area. Deliveries may be deposited outside storage bins and pushed into the bin with a front-end loader.
Block walls that separate sand, topdressing, and rock should be filled solid with concrete. Ceiling fans can help reduce moisture retention, when the storage area is located inside.
Equipment Maintenance & Storage
Equipment storage and maintenance facilities should be designed to prevent accidental discharge of chemicals, fuels, or contaminated wash water from reaching water sources. Properly storing and maintaining equipment also extends the useful life of machines and reduces repairs. Maintenance and preventative maintenance should be completed according to manufacturer’s specifications and recommendations. It is important that communication of equipment-related issues occurs regularly between the equipment operator and equipment manager. Record-keeping for maintenance and repairs (date, operator, maintenance administered, any issues, etc.) is a must for equipment maintenance. Ensure that operators have been properly trained on equipment usage and maintenance; establish ongoing training programs. Ensure all safety devices are in working order.
A list of necessary equipment to properly maintain the golf course must be developed. Maintain a parts inventory and determine proper storage location, include clear labeling for inventory. The size of the equipment is important to determine space requirements. Each piece of equipment should have a designated spot, delineated with colored lines when possible, indicated with its name or number, and parked in the same spot daily. Proper location provides for identification if a leak (oil, hydraulics, etc.) develops and increases accountability for optimal operating conditions.
Facility logistics planning should allow for equipment to be moved in and out of the storage area without unnecessary shuffling of equipment. Overhead doors located on both sides of the equipment storage area can allow for ease when moving equipment (entering or exiting the building) and provide air flow. Overhead fans in the equipment storage area facilitate air flow and help reduce moisture.
Waste oil from equipment should be collected and stored in a container set on containment. If stored outside, there should be a roof over the container and a valve in the bottom to release rainwater.
The equipment maintenance and storage areas provide an excellent location for the shop compressor, eliminating the loud running sound in a personnel work area.
Best Management Practices
Store and maintain equipment in a covered area with a sealed impervious surface to limit risk of fluid leaks and facilitate early detection of small leaks that may require repair
Seal floor drains unless they are connected to a holding tank or sanitary sewer with permission from the local wastewater treatment plant
Store pesticide and fertilizer application equipment in areas protected from rainfall to prevent discharge into soil or water
Store solvents and degreasers in lockable metal cabinets away from ignition sources in a well-ventilated area; these products are generally toxic and highly flammable; never store them with fertilizers or in areas where smoking is permitted
Keep an inventory of solvents and SDS for materials onsite, in a different location that is easily accessible in case of an emergency
Keep basins of solvent baths covered to reduce emissions of volatile organic compounds
When possible, replace solvent baths with recirculating aqueous washing units; soap and water or other aqueous cleaners are often as effective as solvent-based products and present a lower risk to the environment
Always use appropriate PPE when working with solvents
Never allow solvents or degreasers to drain onto pavement or soil, or discharge into waterbodies, wetlands, storm drains, sewers, or septic systems
Collect used solvents and degreasers in containers clearly marked with contents and date
Blow off equipment with compressed air to reduce damage to hydraulic seals
Equipment Washing
Equipment washing guidelines should be established to reduce potential for residues to reach surface waters, groundwater, drainage pipes, or storm sewers. The residues from washing equipment include grass clippings, soil, soap, oil, fertilizer, and pesticides. A contained, impervious area should be dedicated for washing down equipment. It should be kept clean. Closed loop water recycling systems with a proven track record should be utilized. Captured wash water may be used as a dilute pesticide per label instructions.
Grass clippings are important to address when washing mowers. Blow clippings off mowers using compressed air before washing to conserve water and so that clippings do not enter the wash water recycling system. Clippings can be collected and composted or disposed of in a designated debris area.
For equipment with possible pesticide residue, BMPs should be followed to ensure that wash water does not become a pollution source.
Best Management Practices
Brush or blow off grass clippings from equipment using compressed air before washing
Wash equipment on an impervious surface (concrete or asphalt pad) that collects the wash water Once collected material dries, dispose properly
Wash equipment with a bucket of water and a rag to minimize the amount of water used and use only the minimal amount of water required to rinse the machine
Use spring-loaded spray nozzles to reduce water usage when washing
Minimize use of detergents and use only those which are biodegradable, non-phosphate
Consider a closed-loop wash water recycling system
Do not discharge wash water to surface water, groundwater, or susceptible/leachable soils either directly or indirectly through ditches, storm drains, or canals; never discharge to a septic tank
Never discharge to a sanitary sewer system without written approval from the appropriate entity
Washing areas for equipment not contaminated with pesticide residues should drain into oil/water separators before draining into sanitary sewers or holding tanks
Do not wash pesticide-application equipment on pads with oil/water separators; do not wash near wells, surface water, or storm drains
Do not wash equipment on a pesticide mixing and loading pad; keep grass clippings and debris from becoming contaminated with pesticides
Solvents and degreasers should be used over a basin that collects used material
Waste Handling
Proper waste management is important for the health and safety of the public, in addition to conserving natural resources within the state of Wisconsin. Current statewide recycling efforts divert 1.7 million tons of materials out of Wisconsin landfills annually, which results in reduced energy use and pollution. A golf course maintenance facility generates a variety of waste materials including fluorescent or LED lights, glass containers, plastic, tires, metal, paper products, solvents, chemical containers, batteries, used oils, used or contaminated fuel, paints, aluminum cans, and wood. A proper recycling and waste removal program must be deployed to maintain health and safety, plus reduce waste to landfills.
Additional information: https://dnr.wisconsin.gov/topic/Recycling/facts.html
The waste disposal area should be located away from normal employee activity, but close enough to be utilized properly. Proper access for waste pick-up vehicles should be incorporated into the design and location.
Best Management Practices
Measure waste levels and implement source reduction practices to reduce the amount of waste generated in the first place
Have separate areas designated and labeled for recyclables and waste
Educate staff and guests on items which may be recycled; identify ways to increase recycling efforts, including proper signage and communications
Operate equipment properly, adhering to preventative maintenance and manufacturer guidelines to avoid need for repair and prolong lifecycle, minimizing replacement needs
Source environmentally preferred products when possible
Purchase quantities that can be used prior to the expiration date or within six to 12 months of purchase
Label containers for the purpose of storing oils, solvents, degreasers, and fuels
Never dispose of waste down storm drains
Collect used oil, oil filters, and antifreeze in separate marked containers and recycle them as directed by local and state authorities
Antifreeze may be considered hazardous waste by state or local laws and should be handled accordingly; commercial services are available to collect and recycle antifreeze
Properly manage used batteries and fluorescent bulbs as Universal Waste and recycle as soon as feasible
Recycle used tires
Consult an expert in composting for optimal design and processes
Utilize DNR guidelines for hazardous waste disposal and collection services
Local laws and regulations related to disposal of hazardous waste products may vary; become familiar with local laws related to disposal/recycling of these materials
Hazardous Materials Disposal
Ensure all containers are sealed, secured, and properly labeled. Use only FDEP-approved, licensed contractors for disposal.
Wisconsin hazardous waste information and assistance locating local collection services:
https://datcp.wi.gov/Pages/Programs_Services/CleanSweep.aspx
https://datcp.wi.gov/Documents/CleanSweepSchedule.pdf
Pesticide Containers
Empty pesticide containers are classified as hazardous wastes if not properly rinsed. Federal law (FIFRA) requires pesticide applicators to triple-rinse all empty pesticide containers before taking other container disposal steps. Under the federal Resource Conservation and Recovery Act, or RCRA, a pesticide container is not empty until it has been properly rinsed. The improper disposal of a hazardous waste can result in fines and/or criminal penalties. Pesticide containers that have been properly rinsed can be handled and disposed of as nonhazardous solid waste.
Reference https://datcp.wi.gov/Documents/HTCLandscape.pdf and Responsible Pesticide Management for additional BMPs for waste generated from pesticide activities.
Used Oil, Antifreeze, and Lead-Acid Batteries
Collect used oil, oil filters, and antifreeze in separate marked containers and recycle them. Oil filters should be drained (puncturing and crushed) and transported to a place that recycles used oil or to a hazardous waste collection site. Antifreeze must be recycled or disposed of as a hazardous waste using commercial collection services. Do not mix used oil with used antifreeze or sludge from used solvents.
Lead-acid storage batteries are hazardous waste; used acid from these batteries contains high levels of lead and must be disposed of as hazardous waste, unless the acid is contained within a battery being recycled. Make sure caps are in place to contain the acid and store batteries on an impervious surface, under cover if possible. Used lead-acid batteries must be recycled to be exempt from hazardous waste regulations.
Solvents and Degreasers
Routine discharge of small amounts of solvents over time can create environmental and liability consequences, due to accumulation of contaminants in soil or ground water. The EPA and FDEP can deem a “small quantity generator” of hazardous waste based on disposal of as little as 25 gallons per month of used solvents, triggering regulatory reporting requirements. Whenever practical, replace solvent baths with recirculating aqueous washing units (which resemble heavy-duty dishwashers). Soap and water or other aqueous cleaners may be as effective as solvent-based ones.
Using compressed air to blow off equipment instead of washing with water can be easier on hydraulic seals and lead to fewer oil leaks. Store solvents and degreasers in lockable metal cabinets in an area away from ignition sources (i.e., welding areas or grinders), and provide adequate ventilation. They are generally toxic and highly flammable. Never store them with pesticides or fertilizers, or in areas where smoking is allowed. Keep basins or cans of solvent covered to reduce emissions of volatile organic compounds and fire hazards. Keep an inventory of solvents stored and the SDS for each on premise, but not in the solvent storage area. Emergency response equipment recommended by the solvent manufacturer should be kept in an easily accessible place near the storage area, but not inside the area itself.
Follow OSHA signage requirements. Always wear appropriate PPE, especially eye protection, when working with solvents. Never allow solvents to drain onto pavement or soil, or discharge into waterbodies, wetlands, storm drains, sewers, or septic systems. Solvents and degreasers should be used over a collection basin or pad that collects all used material. Most solvents can be filtered and reused.
Store collected material in marked containers until it can be recycled or legally disposed of. Solvent disposal organizations provide solvent washbasins that drain into recovery drums and pickup service to recycle or properly dispose of drum contents. Collect used solvents and degreasers, place them into containers marked with contents and date, prior to pick up. Never mix used oil or other liquid material with used solvents. Use only FDEP-approved, licensed contractors.
Composting
Most composting on the golf course is green waste which includes grass clippings and debris, such as leaves, or routine, healthy landscape trimmings that would normally go to a landfill. Composted materials can be used effectively to improve the soil for topdressing, non-putting surface areas, and donated or sold to offsite vendors. Do not compost diseased material.
In addition, the clubhouse food and beverage department may engage in food waste composting.
More information on composting in Wisconsin:
Recycling: Paper, Plastic, Aluminum, Glass, and More
Paper, cardboard, #1 and #2 plastics, aluminum, and glass should be recycled. Electronics may also be recycled through local providers which may be found through the DNR at https://dnr.wisconsin.gov/topic/Ecycle. Containers for recycling aluminum cans and plastic bottles should be placed in convenient locations on the golf course.
Fuel Facilities
Fueling facilities should be designed, constructed, maintained and monitored to local or state codes. Proper fueling sites have impervious surfaces, spill containment and recovery facilities, located away from surface waters and water wells. Floor drains should be eliminated or removed unless they drain to containment storage tanks or pits.
Check codes for regulations on storage tanks; aboveground storage tanks (AST) is the preferred storage method because it is easier to monitor for leakage. An underground storage tank (UST) must have leak detection monitoring for compliance. Leaks or spills must be contained or cleaned up immediately. Title 40, Section 112 of the Code of Federal Regulations (CFR) requires a Spill Prevention Control and Countermeasure (SPCC) plan for facilities with total aboveground petroleum product storage (i.e., new oil, used oil and fuel) capacity in excess of 1,320 gallons. SPCC plans can help minimize the potential for a petroleum leak or spill to occur and mitigate environmental impacts. SPCC regulations generally require secondary containment for filling and dispensing operations; alternatives are allowed if secondary containment is impractical.
Best Management Practices
Locate fuel storage tanks above ground, on impervious surfaces under roofed areas, when possible
Areas should be equipped with spill containment and recovery facilities
Keep a log of fuel added and discharged
Visually inspect the tank for leaks and document in an inspection log
Place automatic shut off valves away from the tanks in case of emergency
Post “No Smoking” signs near the fueling facility
Properly and clearly label fuel storage tanks